
Acceleration (0 - 100 km/h)
< 4 seconds
Top Speed
210 km/h
Fuel Cell Power
105 kW (141 hp)
Boost Power
220 kW (295 hp)
Weight
1250 kg
Size
475 x 190 cm
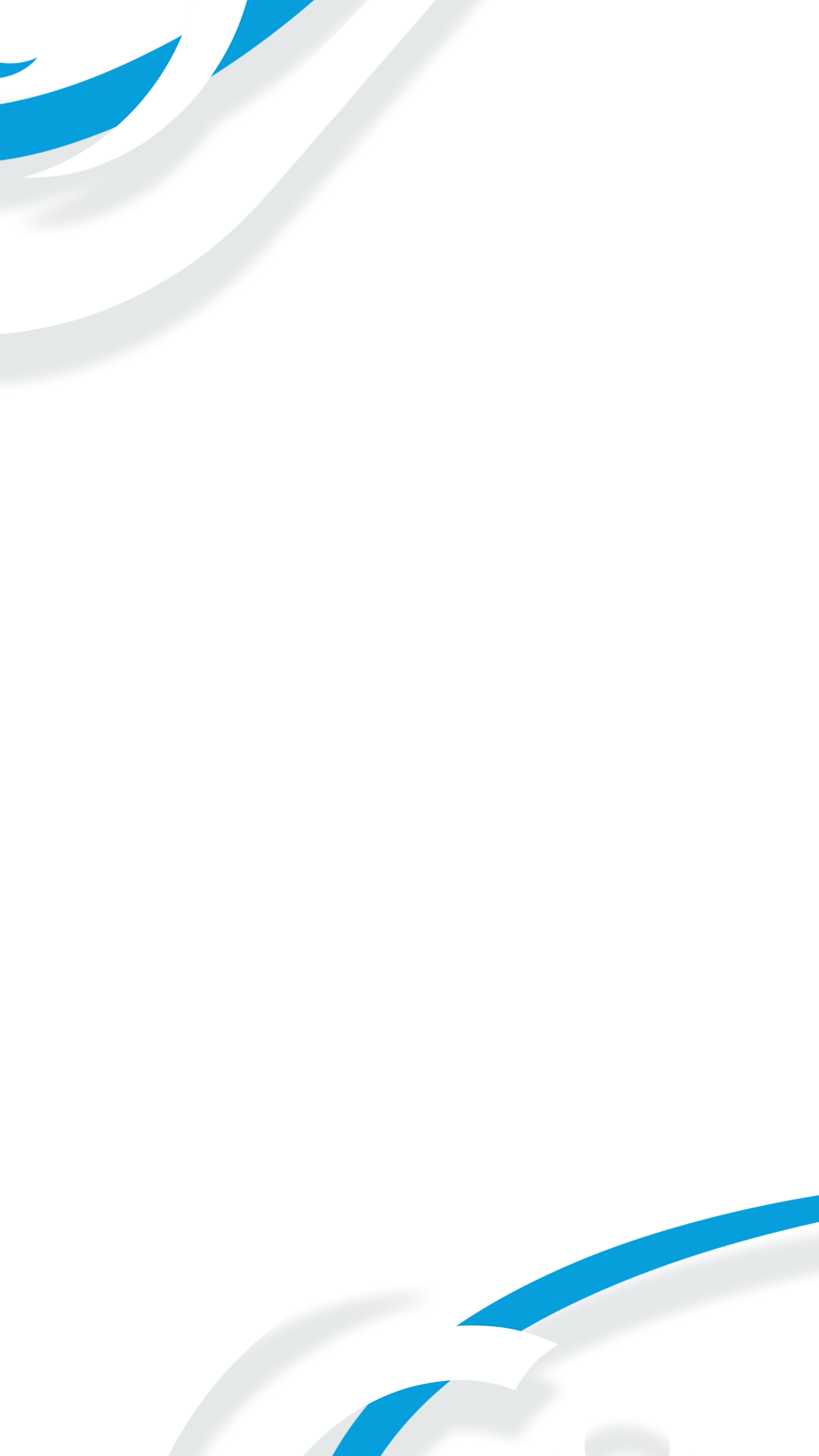
Forze VIII.
Upgrading performance.
After the world debut of hydrogen electric racing by the Forze VII, there was still a lot of work to do in order to win races. Therefore, the Forze VII was stripped down to nothing but the LMP3 monocoque in 2017. From that state she was completely rebuilt with new and better components. Some of the major projects were: implementation of a 700 bar hydrogen system, completely new front and rear suspension, total redesign and production of the electrical wiring harness, and obviously a completely new carbon fibre bodywork for much higher aerodynamic efficiency. Furthermore, the packaging of all components was drastically changed to improve the car’s performance.
Due to all of these huge upgrades, the Forze Hydrogen Racing Team has been able to celebrate their first podium during a race! Furthermore, it became the fastest hydrogen car in the world in 2019.

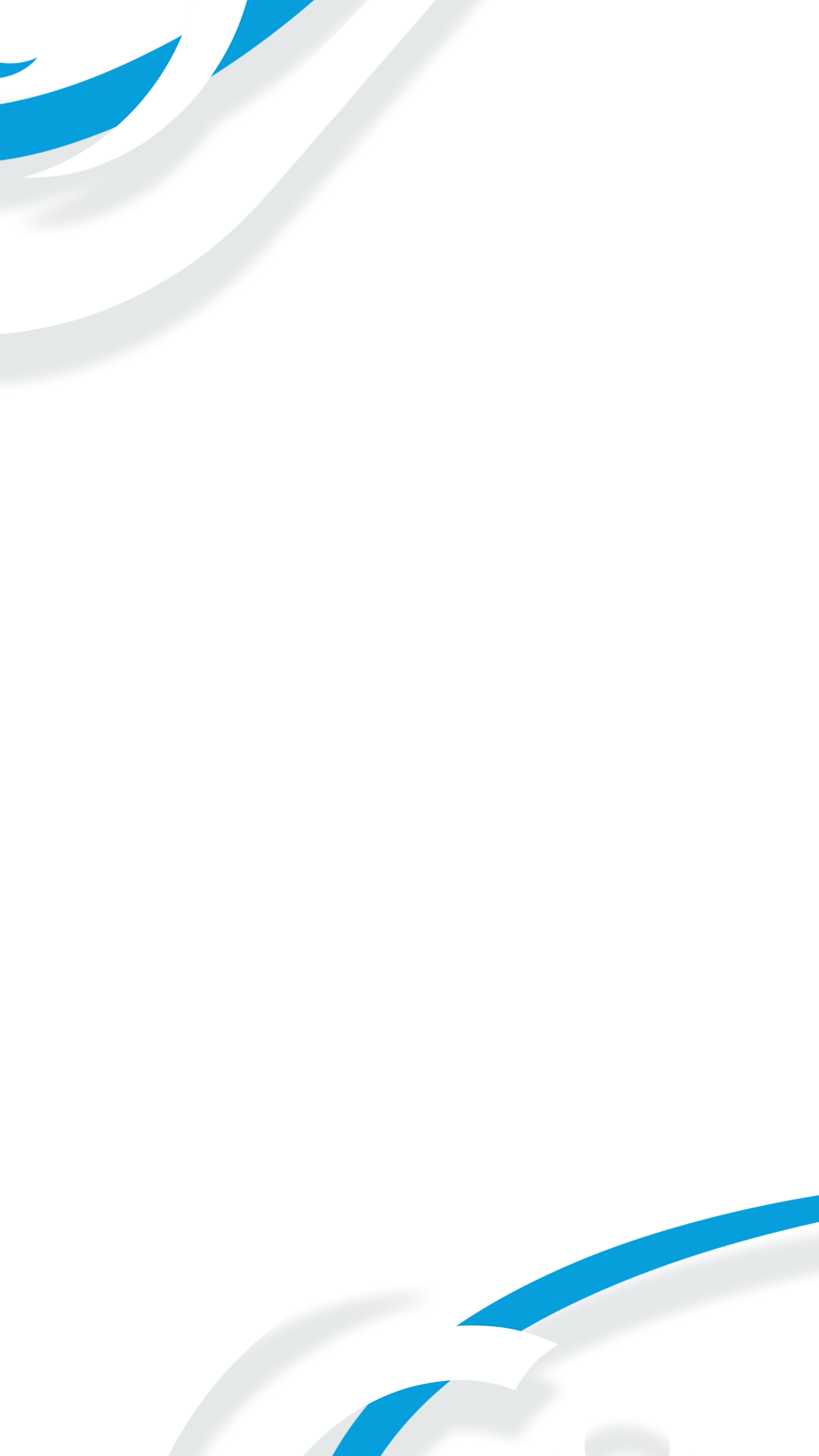
Goals.
Why the hydrogen race car was built.
The Forze VIII was built to compete – and win – against petrol powered cars, specifically in the sport class of the Benelux Supercar Challenge.
The Supercar Challenge race weekend at the Gamma Racing Days consists of a free practice session and qualifying on Friday, a 60 min race on Saturday and a 45 min race on Sunday.
Even though the Forze VIII has a 700 bar refueling option implemented, it is not allowed to refuel hydrogen gas on track during the race. This is unfortunate, as quick refueling is one of the major advantages of hydrogen over for example battery electric vehicles. Luckily, another advantage of hydrogen in mobility is high endurance. The brand new 700 bar fuel tanks provide us with enough capacity to finish the race without refueling. Competing in the Supercar Challenge has demonstrated the potential of hydrogen and the future of sustainable racing!
In the Future, it is Forze’s goal to participate in higher classes of the Supercar Challenge such as the Prototype and GT class. In the long term, we plan to move towards endurance racing.

Achievements.
What we have accomplished.
The Forze VIII became the first hydrogen race car in history to compete in a FIA certified race. On August 18th 2018, she raced in the sport division of the Supercar Challenge against petrol-powered supercars.
In August of 2019, Forze celebrated its greatest achievement yet. The Forze VIII competed in the Supercar Challenge at the Gamma Racing Days again and came in 2nd in our class. This success highlighted the capability of the team and makes us even more excited to see what the future has in store for us.
On the circuit of Zandvoort, the Forze VIII holds the official lap record for electric sports cars at 1:55.809 during a test where conditions were far from ideal. On the TT Circuit Assen, the unofficial lap record of the Forze VIII is 1:56.958.