
Acceleration (0 - 100 km/h)
< 4 seconds
Top Speed
210 km/h
Fuel Cell Power
100 kW (135 hp)
Boost Power
190 kW (258 hp)
Weight
1100 kg
Size
460 x 190 cm

Forze VII.
Innovating a new era.
In August 2017 the Forze VII made the world debut of hydrogen electric racing. Never before had a hydrogen electric car competed in an official race. Forze competed in the Supercar Challenge at the Gamma Racing Day. By competing with gasoline powered cars Forze proved that this technology is feasible, reliable and very exciting.
The Forze VII is built around a LeMans Prototype (LMP) monocoque. LMP cars are the fastest endurance race cars. Therefore the monocoque will not only be the foundation of this car, but also the basis as Forze looks to the future.
This allowed the team to develop even better race cars and keep setting records!
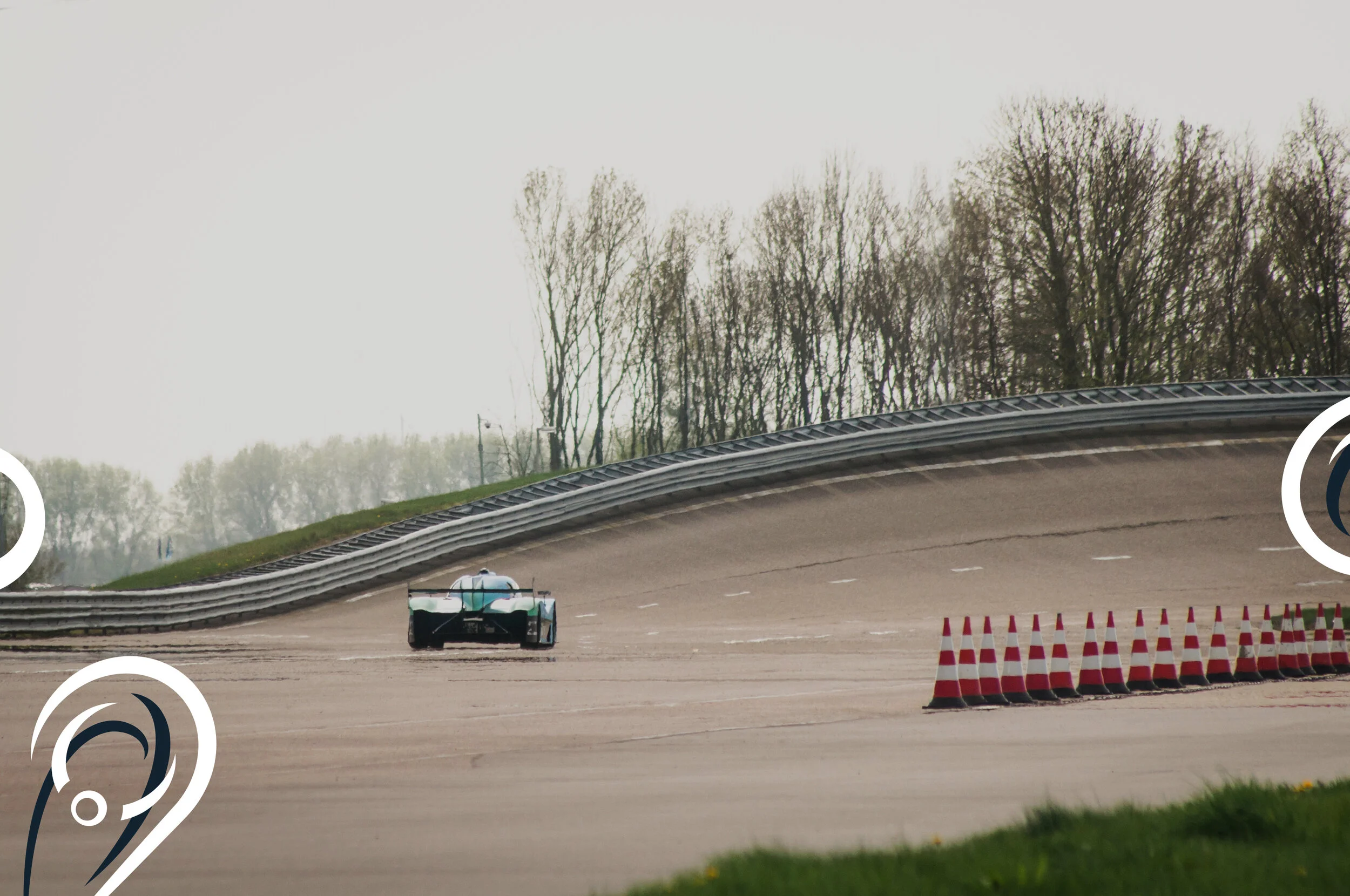

Overview.
Of the Forze VII
The Forze VI has set many lap records and was thus one of the fastest hydrogen electric cars in the world.
The only thing she did not do was competing in race against gasoline powered cars. Forze VII was built with this goal in mind. Continuing and innovating on the base which was set, the team developed a complete new race car with the ultimate goal of winning in an official race! In August 2017 the Forze VII made the world debut of hydrogen electric racing. Never before had a hydrogen electric car competed in an official race. Forze competed in the Supercar Challenge at the Gamma Racing Day, Europe’s largest combined event in auto- and motorsport. By competing with gasoline powered cars we prove that this technology is feasible, reliable and very exciting.

Achievements.
What has the car accomplished
On the 7th of August 2017 the Forze VII became world’s first hydrogen electric race car to compete in a race. It raced against fossil fueled cars in the Supercar Challenge. By setting a third laptime, the potential of hydrogen technology was proven. For this achievement Forze was awarded with the Garage 56 trophy of the Supercar Challenge and the 3rd place of the D:DREAM Innovation Award.
The Forze VII lapped the circuit of Zandvoort in 1:56.76 and the TT Circuit of Assen in 1:57.288.